You're probably familiar with the term OBD-II and aware that it's a system associated with late-model cars and trucks, but you might not fully understand the concept. In its simplest form, "On-Board Diagnostics" describes an on-board computer, which controls engine functions and has the capability of detecting faults in data inputs, outputs (commands), and subsystems. When a fault is detected, a warning indicator illuminates on the instrument panel and a diagnostic trouble code (DTC) is stored in the computer's memory bank. This DTC then aids technicians in troubleshooting the cause of the problem.
Without getting too much into Ohm's law, let's take a look at a simple data input failure. An engine coolant temperature (ECT) sensor is a thermistor that varies electrical resistance with temperature. The powertrain control module (PCM, ECM, ECU) sends out what we call a 5V reference signal on one of the two wires connected to the sensor. The second sensor wire is routed to vehicle ground. As coolant temperature changes, the resistance between the 5V reference and ground also changes; this causes the 5V reference voltage to vary up and down (voltage drop). The PCM views this voltage, translates it to a coolant temperature reading, and uses the information to help run the engine more efficiently.
Now imagine that a not-so-friendly rat makes his way under the hood and chews through one of the ECT sensor wires. Since there's no longer any path to ground for the reference signal, the PCM is now viewing the full 5V. This voltage is out of a normal coolant temperature sensor range, so the PCM detects the problem, turns on the malfunction indicator lamp (i.e. MIL, check engine, service engine soon), and stores DTC P0118— engine coolant temperature circuit high input.
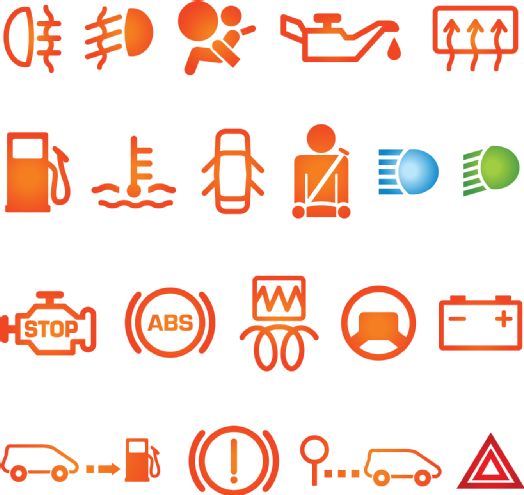
| Understanding On Board Diagnostics DASH LIGHTS
This is easy stuff, right? Not always. The same DTC can be caused by a bad sensor, a poor connection, or even an internal PCM failure. Further diagnosis is often necessary, so each DTC has a diagnostic flow chart to help pinpoint the exact cause of the problem. A common snag is an intermittent MIL/DTC, such as a marginal connection, which only sets P0118 monthly under certain temperatures and driving conditions.
The EPA's Clean Air Act introduced federally mandated automotive smog regulations in 1970, leading to the development of OBD in the 1980s and 1990s. Leaner air/fuel ratios and embryonic pollution control devices stifled engine power, within a timeframe where overall vehicle quality was lacking. Not a happy era for the auto industry.
Earliest OBD systems go as far back as the late 1960s with minimal capabilities of retrieving computer data on a few fuel-injected engines. But in 1980, General Motors took a big step in the U.S. market with the implementation of the assembly line diagnostic link (ALDL). This was an electrical connector where PCM data could be retrieved on the assembly line for test purposes. The ALDL models began in California but were part of GM's nationwide production by 1981. At this point, technicians could not pull real-time data from the ALDL with a scan tool but could jump two of its terminals and retrieve DTCs by the flashing sequence of the MIL.
These earlier systems are now referred to as OBD-I. The drawback was a lack of uniformity. Manufacturers used different DLCs (data link connector), communication protocols, and DTCs. Technicians were eventually able to retrieve real-time serial data from the DLC with the correct scan tool. However, it required multiple adapters and service information to plug-in and decipher data from all the different makes and models.
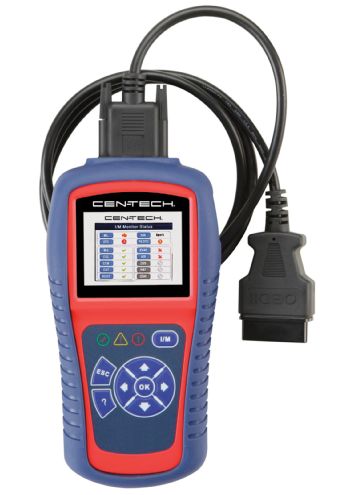
| Understanding On Board Diagnostics OBD Ii Reader
The brainstorm of a universal OBD-II system originated with a recommendation by the Society of Automotive Engineers (SAE), then enforced by The California Air Resources Board (CARB) and the EPA. By 1996, OBD-II was mandatory for all cars and light-duty trucks sold in the U.S. This meant every vehicle used the same DLC located within reach from the drivers seat, a universal list of diagnostic trouble codes was established, and communication protocols were agreed upon. So anyone with the appropriate OBD-II scan tool could plug into any of these U.S.-sold vehicles andd view engine control data and publically known DTCs.
Motivation behind OBD-II was not only to aid owners and technicians with repairs but also to produce a more efficient means of running state emissions inspections. Originally, most state inspections in highly populated areas required an emission analyzer probe stuck in the tailpipe. If the engine was running clean at idle, you were good-to-go. The problem was that engines could very well be giving off excessive amounts of carbon monoxide (CO), hydrocarbons (HC), or oxides of nitrogen (NOx) into the atmosphere off-idle under normal driving conditions. So the EPA came out with acceleration simulation mode (ASM). The ASM test procedure runs the vehicle on a dynamometer to test emissions output during acceleration and under a load. This creates a more accurate simulated driving environment and uncovers previously undetectable faults. Full-time 4WD vehicles that cannot be run on the two-wheel dynamometer are instead subject to a two-speed (high and low RPM) test in Park. Keep in mind that emissions inspection requirements are based on federal regulations but administered by state agencies and vary by region.
With the implementation of OBD-II, most emissions inspections on vehicles 1996 or newer no longer require the emissions analyzer or a dyno. Regulations are now somewhat trusting of the onboard data streaming out of the DLC. The rationale was if the OBD-II system sees no fault, pollution out the tailpipe should be within specifications. Plug the inspection machine into the DLC, observe no problem found, and the vehicle passes state inspection—almost.
A couple of visuals are still part of emissions inspections. No emissions control component or system should be missing, modified, or disabled. The MIL must come on with the ignition but off following engine start-up. The gas cap may also be tested to hold sufficient fuel-tank pressure, but this task is being phased out with new production due to OBD technology that can accurately detect evaporative emissions leaks (fuel vapor/hydrocarbons).
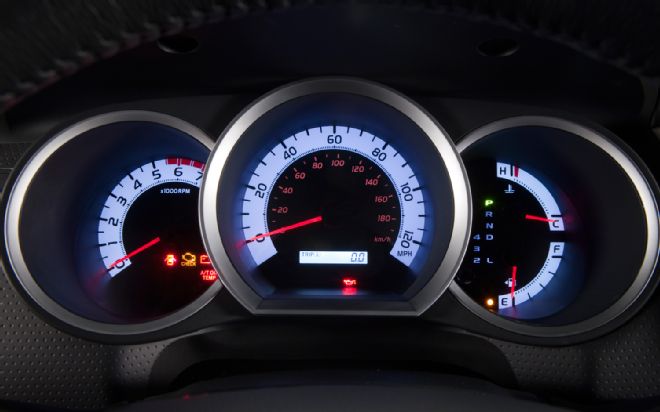
| 2012 Toyota Tacoma Dash Guages
Ever gone in for a state emissions inspection after a recent dead battery or a DTC being cleared following a repair and failed? Non-continuous readiness monitors were the cause and another important aspect of OBD-II. Non-continuous readiness monitors are automatic self-tests performed by the PCM on emissions related component and subsystem operation. Gas engine non-continuous monitors include catalyst (CAT), heated catalyst, evaporative (EVAP) system, oxygen (O2) sensor, oxygen sensor heater, EGR (exhaust gas recirculation), and (VVT) variable valve timing.
The hard failure of an ECT sensor circuit (P0118) described earlier was detected by a continuous monitor. The PCM was constantly viewing the data and detected the fault almost immediately after the rat caused an open circuit and the ignition was turned to the On position.
Non-continuous readiness monitors are more complex tests which analyze the performance of emissions-related systems, often by sending out commands and viewing the resulting input data. When the PCM loses memory due to loss of battery voltage, clearing of DTCs, or software reprogramming, the status of these readiness monitors go back to "not ready" or "incomplete." Successful employment of these tests often requires one or more completed "drive cycles" (key on, key off, and everything in between). A drive cycle can vary by the specific monitor, make and model, and may require engine startup within a specific temperature range, vehicle driven for a certain period of time, at determined speeds, etc. Once a readiness monitor has been completed with no problems detected, status is then "ready" or "complete." If a problem is found, the MIL comes on and a DTC is recorded.
Let's say a vehicle owner is aware of an emission-related OBD-II failure, but the problem is a deteriorated catalytic converter that requires a somewhat long-term drive cycle before the readiness monitor determines a fault and sets a DTC. The "not ready" status of the catalyst readiness monitor may prevent the vehicle from passing inspection, even if the DTC was cleared on the way to the inspection station.
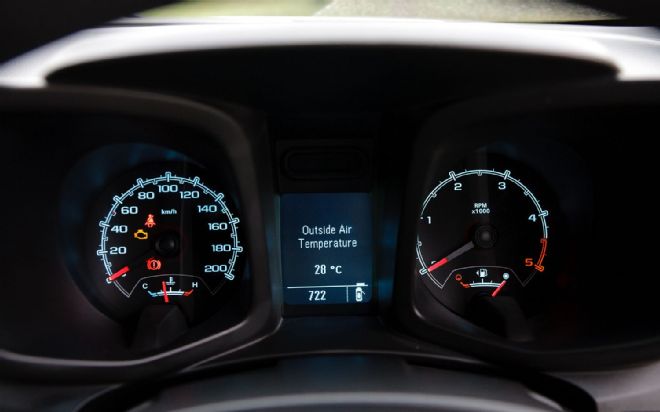
| 2012 Global Market Chevrolet Colorado Dash Guages
Although readiness monitors can prevent fraudulent passing of emissions inspections, the EPA does leave a window to prevent unnecessary inconvenience for drivers. Model years '96-'00 can pass with two monitors not ready, while '01 or newer require no more than one monitor incomplete. All may be mandatory in the near future, but the evaporative emissions (EVAP) monitor seems to be a stumbling block. Due to the temperature ranges needed to conduct the required drive cycles, local climate can prevent completion for an extended period of time.
The number and detail of diagnostic trouble codes has increased significantly over the years. This helps in troubleshooting the consistent advancement in automotive systems. OBD-II DTCs are broken down into four main categories. All DTCs begin with the category letter, followed by four numbers: "Pxxxx" for powertrain, "Bxxxx" body, "Cxxxx" chassis, and "Uxxxx" communication network. The second character will be 0 (generic, common to all OBD-II systems), 1 (manufacturer specific), and 2 and 3 (influenced by the SAE). The third character represents a breakdown of subsystems, the fourth and fifth deal with the specific failure.
Last example with the rat: P0118 is a powertrain DTC; the most common category dealt with by drivers involving both engine and transmission operation, and the only DTCs effecting emissions inspections. P0xxx tells us it's a generic OBD-II trouble code. P01xx –emissions management (fuel and air). P0118—ECT sensor circuit high input. Typically, B, C, and U DTCs will not turn on the MIL and are used primarily by dealership technicians for advanced diagnostics on the non-powertrain related systems.
The MIL is the sole part of OBD-II viewed by drivers, often referred to as the check engine light, and mostly displayed as an engine-outline icon. The MIL coming on with the ignition and off when the engine starts, tells us the PCM is functional. The MIL on solid while the engine's running indicates there's a system failure and a DTC exists. But the MIL flashing with the engine running is a red flag. This warns the driver that a component failure (typically a misfire) can damage the catalytic converter(s) due to excessive fuel (hydrocarbons) in the exhaust. Should this occur, keep road speed to a minimum and get the vehicle to a repair shop as soon as possible.
Write To Us!
If you have a technical question regarding your pickup, SUV, or van, feel free to contact us! Send a letter care of Truck Trend Garage, 831 S. Douglas Street, El Segundo, CA 90245, or e-mail us at trucktrend@sorc.com. Due to the volume of questions received every month, we cannot guarantee that everyone's question will be personally answered or will appear in the magazine.
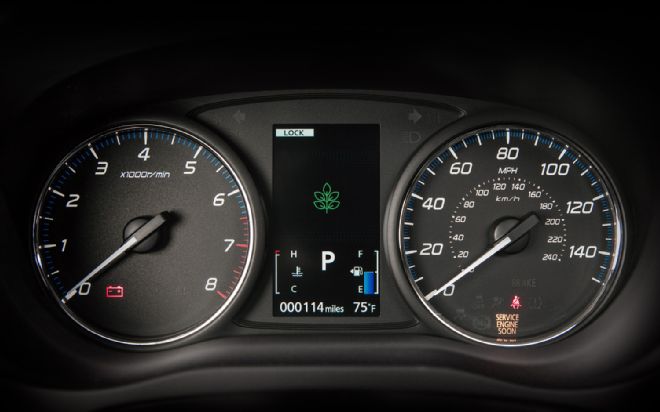
| 2014 Mitsubishi Outlander Dash Guages