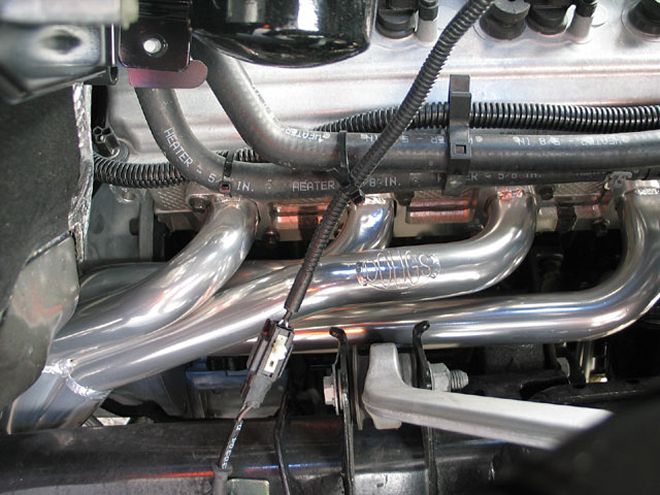
| exhaust System exhaust
Next to the suspension, the exhaust system of your gasoline-fueled four-cycle truck engine is perhaps the most misunderstood bolt-on performance combination on the market. The basic concept of less-restrictive flow is pretty well understood, and that's what most systems promise: less backpressure and less restriction to airflow to get more power from your engine. True, there are some issues with how the engine management systems of each brand respond to the increased airflow, but generally, these parts make a predictable amount of power from the increased mass airflow through the engine.
In discussing the exhaust system, we should first answer the basic question of what, exactly, an exhaust system does.
Two things: First, it routes the heated gas generated during the compression stroke as fuel and air burn in the cylinder, away from the passenger compartment, which is a good thing since several of its chemical components - particularly carbon monoxide - are toxic; second, if properly designed, it can increase the power output of an engine.
How Does an Exhaust System Improve the Power Output of an Engine?: In the simplest terms, it increases the mass airflow through the engine by improving the volumetric efficiency (VE) of the engine and by reducing pumping losses on the exhaust side.
Volumetric efficiency is defined as the actual volume of air that the engine captures in its cylinders divided by the physical size of the swept volume of the cylinder and combustion chamber. In other words, if a cylinder has a swept volume of 37.5 ci and it only pulls in 18.75 ci, we say it is 50 percent volumetric efficient; for 100 percent VE, it'd take in 37.5 ci.
Pumping losses refer to the power used to pump the mass in and out of the engine. A portion of the engine's power is used to generate a pressure drop in the cylinder on the intake stroke that is filled to the extent of the cylinder's volumetric efficiency by the higher pressure of atmosphere (about 14.7 psi at sea level for standard conditions). A portion of the engine's power is also used to force the leftover gas from the combustion process, out of the combustion chamber, through the exhaust port, down the exhaust system, and finally, out into the pressure of the atmosphere.
How Does the Exhaust System Improve Each Cylinder's Volumetric Efficiency and Reduce Pumping Losses?: Most of the improvement in VE comes from using the energy of the exhaust pulse to help evacuate the cylinder and begin the process of filling it during overlap (when the exhaust valve pops open just before the intake valve closes), a process engine tuners call the scavenging effect. The scavenging effect occurs when a negative pressure pulse is created behind the exiting gas, helping to suck the remaining spent gas from the cylinder.
Modern cam designs open the exhaust well before the piston reaches bottom dead center. This does two things. First, because the exhaust gas is hotter and therefore exerts more pressure within the cylinder than it would be later in the power stroke, when the exhaust valve opens the higher pressure is used to accelerate the mass of the exhaust gas, which by itself helps evacuate, or blow down, the cylinder. Second, by opening the exhaust valve while the intake is open, the negative pressure wave behind the exiting exhaust pulse helps pull the intake charge into the cylinder. A properly designed exhaust system will enhance this process.
Header and exhaust system designers use the diameter and length of the header runners and the exhaust to tune the system to the engine combination. Historically, engines are most sensitive to changes in the diameter of the primary runner; this is the exhaust tube that is fastened to the engine head at the exhaust port. The primary diameter seems to establish the horsepower peak, while the length of the primary tube tends to control the rpm range where the torque peak occurs. In general, a longer primary shifts the power peak to a lower rpm and vice versa. Of course, this relationship doesn't always hold true for every engine and application.
The goal of the header designer is to tune the travel of the negative pressure pulse of one cylinder so it hits the port of the next exhaust event of a different cylinder. How well this is accomplished determines to a large degree the power curve of your engine.
Building a good exhaust header and system is quite an artful application of science. It's all about synchronizing a sound wave and a rapidly cooling, and therefore shrinking and slowing, exhaust gas pulse traveling down the tube with another cylinder and its valve timing events. Keep in mind that when the exhaust valve cracks open, a sound wave punches out of the exhaust port at the speed of sound, approximately 18,500 inches per second, followed by the exhaust gas slug at about 3,600 inches per second. If the design is correct, when the high-pressure part of the sound wave passes through the collector, it is creating a low-pressure condition that reaches back through the other tubes and "pulls" the next exhaust pulse out of the cylinder, or at least offers less resistance than otherwise to the exiting gases.
Which Header Design Makes Most Power?: A 4-into-1 header with a fine-tuned collector tends to create the most peak power of any header design. To make this design work, you have to introduce the primary tubes into the collector stacked: two on the top, two on the bottom. It doesn't work if you collect the tubes side by side; this causes ground clearance and routing problems for some vehicles. The next best solution is a 4-2-1 design, which gives more ground clearance as well as requiring less room to route through tight engine compartments. The downside is you loose a little power. When matched with the properly sized tube diameters and length for your combination, you're typically within about 3 to 5 hp, depending on engine size, of what a similarly matched 4-into-1 system would do.
Whether it's a 4-2-1 or a 4-into-1 header, the basic tuning theory of small-diameter long tubes for torque and larger-diameter short tubes for high-rpm horsepower typically holds true. However, there are always exceptions, especially with 4-2-1 headers because you have the secondary tubes to play with as well as the primaries.
Shorty headers are generally better than stock, but be very careful when choosing this design for a modern engine. The factories are designing very efficient engines with equally efficient exhaust systems.
Ultimately, an exhaust header can only be tuned to be really effective within a fairly narrow rpm range, say around 1,000 rpm. So you need to choose a header design that works with your combination. For example, don't use headers tuned to make power at 3,000 rpm if your engine has a wicked mega-duration, high-lift, high-rpm cam with head porting.
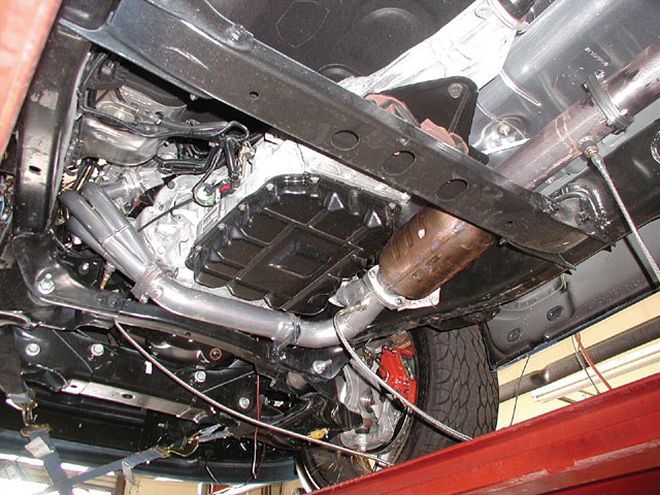
| Here's the test probe setup used to tune the exhaust system. The pressure sensors measure the pressure pulses in the header collector, at the Y-pipe before the catalyst, and in the exhaust system after the catalyst.
After the Collector: After the header collector and the catalyst, the goal is to reduce the resistance to the exiting gasses by the exhaust system. The resistance in the exhaust system comes from several sources: drag from the surface area within the exhaust system, for example, as well as all the twist turns in the exhaust system. Each time the exhaust system forces the mass in the exhaust to turn, it requires energy. Designing an exhaust circuit with the least amount of turning possible, given the limitations of having to work around the structures of your truck, reduces resistance to flow caused by the inertial losses. You can reduce the drag caused by the surface area by reducing the length of the system. An open header or the "zoomies" on a dragster are examples of systems that use both tactics, as is the use of wider radius bends in aftermarket performance after-cat exhaust systems. Of course, you have limits to how far you can shorten the exhaust system on a street-driven vehicle, but if you're after the last bit of power, it's a place to look.
Another tip for exhaust system performance is to look for a low-pressure area in which to dump the exhaust. This is one of Smokey Yunick's, famed pioneer NASCAR mechanic, "secrets." On street-driven vehicles, most people just choose the safest and most cosmetically pleasing location to put the exhaust tips. But again, if you're looking for performance, here's another place to find some.
More Info: We've presented only the basics of performance exhaust. There's more to it and much to learn. For example, we didn't mention step headers or the super-heated solid pulse model some engine design software models use. But this should give you at least a clue, and you can always contact the exhaust system sources that support this magazine. They're working with this stuff constantly and have the latest information on what works and what doesn't.
Divide And ConquerTesting Doug's Headers' Divided Collector DesignJust to show you how weird designing exhaust systems is and the unexpected ways you find power, the process is captured here. Doug's Headers was in the middle of developing a header and a dual exhaust system for the late-model Hemi Ram 1500 pickups. The company worked in conjunction with the guys at Kenne Bell, which provided Dynojet time as well as rigging up pressure sensors at key points in the exhaust system as they tested and developed the package.
It's a subtle art designing exhaust system components as witnessed by the claimed advantage of a divided collector header design. Here's how the numbers shook out on the DynoJet in a series of Second gear pulls:
Stock trim: 263 hp Doug’s Headers, stock exhaust: 275 hp Doug’s Headers; Doug’s exhaust: 283 hp Remove Cat 287 hp Add Pulse Divider in Collector: 290 hp Open Header w/ Divider(third gear pull): 293 hp The results and the pressure traces below show the effects of the harmonics and resonance frequency changes as the engine sweeps through its rpm range. Internal combustion engines are pulse flow devices, so in reality, you don't have a smooth flow of intake or exhaust. There's an acoustic energy component to the exhaust that can be tuned. The divider seems to work reasonably well with an open header.