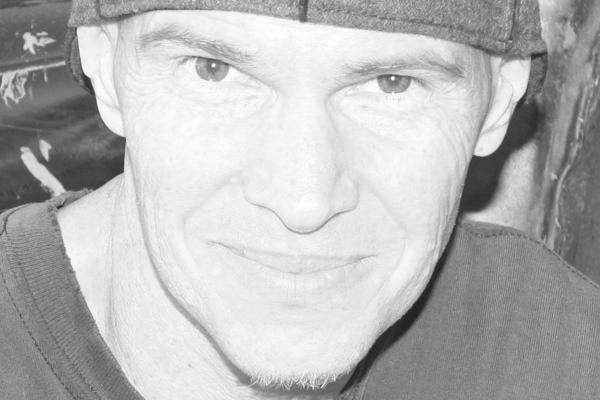
Kevin Blumer
Contributor
Trailing arms are the most visually striking component of a linked rear suspension. In addition to connecting the chassis, rear axle, and shocks, they provide fabricators with an opportunity for artistic expression. We’ve seen some intricate designs, along with some simpler stuff, and have been positively impressed with it all.
A trailing arm has a big job to do. First, it’s got to provide an unyielding link between the chassis and the rear axle. Next, because the shocks are mounted to it, it must support the weight of the vehicle as well as the tension and compression forces generated between the rear wheels and the chassis. Finally, trailing arms need to be strong enough to withstand random hits from terra firma: rocks, roots, and plain old dirt.
With the duties of a trailing arm in mind, it’s obvious that function has to come first. If a trailing arm can look nice, too, then that’s an added bonus. Function first, and then form.
Follow along as we explain the how and why of trailing arms.
Step By Step

1. Though the terms “trailing arm” and “link” or “lower link” are often used interchangeably, we’d like to be more specific with our terminology. You’re looking at upper and lower links on the rear suspension of a Jeep JK Wrangler. Because the shocks do not mount to the links, they don’t have to support any chassis weight. These links are simply tubing with a suspension joint at each end. When we speak of “trailing arms,” we’re talking about lower suspension links to which shocks are mounted. Fair enough?

2. Most trailing arms are made from a combination of tubing and plate. These trailing arms were designed by Dan Barcroft and are 100-percent chromoly plate. Laser-cut by Elite Laser Cutting, they were welded together by the author. If they look intricate, that’s because they are.

3. These parts are for creating a welding jig. They’ll be welded to a piece of boxed steel tubing, and then the trailing arms will be put together using the jig.

4. The sided faces of the trailing arms were used to help locate the jig parts on the boxed tubing.

8. The heat of welding will always produce some distortion, no matter how many times you skip from place to place while welding, and no matter how much time you allow the part to cool between welds. When the trailing arms were ready to be removed from the jig, even a sledgehammer wasn’t able to budge the mounting bolts at each end. It was necessary to cut through a bolt instead.

5. The shock-mounting pocket was a very involved aspect of these trailing arms. The shocks mount below the centerline, but more on that later. There are tons of triangles built into these trailing arms. As is true with a rollcage, triangles add strength.

9. A strip at each end wraps around the outside of the uniball cup and provides an additional measure of strength and safety. Those tabs are for a “catch strap” that’s attached to the chassis and will keep the front end of the trailing arm from digging into the ground should the forward mounting bolt fail.

6. The internal tabs weld onto the top, bottom, and side plates. On the top and bottom, the welds were layered on top of each other until they were above the flush surface of the plate. Then the top and bottom plates were ground smooth in the name of aesthetics.

10. Did we mention the shock pockets were labor-intensive? These trailing arms will be heat treated before they’re put into use, hence, the vent holes drilled into every chamber that could potentially trap hot air.

7. These trailing arms use spherical bearings/uniballs on both ends, but you don’t want to weld the uniball cup in place with the spherical bearing inside it because you could cook the bearing’s Teflon liner in the process. To help the uniball cups keep their shape during welding, machined spacers were created to snap in place, absorb heat, and hold proper dimensions.

11. Fully welded, and ready for heat treating: Most trailing arms are not heat treated, and seem to do just fine without this extra step. If you’re building with a heat-treatable steel alloy, and you want the ultimate in strength, heat-treating is worth looking into. If you are fabricating your own trailing arms, do yourself a favor and build them to mount two shocks, even if you have to start with coilovers only. Trust us: You will want the performance of bypass shocks later on.

12. Excessive twist can be a problem when spherical bearings (in the form of uniballs or rod ends) are used on both ends of a trailing arm. There are a few ways to counteract this negative trait. One is to use a wobble-stopper uniball at the frame end of the link. The wobble stopper is simply a uniball assembly that features an external twist limiter, usually in the form of a custom-machined spacer made from nylon or Delrin. Blitzkrieg Motorsports and Kartek Off-Road both offer wobble-stopper uniball assemblies as stand-alone builder parts.

13a. Another anti-twist tactic is seen on Brandon Arthur’s F-100. Imagine a line drawn through the center point of the front and rear trailing arm pivots.

13b. When the shocks are mounted below that center line, the trailing arms will self-straighten during compression. Twisting during rebound is minimal and does not damage the trailing arm or the shocks.

14. When the shocks are mounted above the center line, as seen here with an S.I. Motorsports Ranger four-link kit, the forward-most pivot must be made so as to control the twist.

12 Excessive twist can be a problem when spherical bearings (in the form of uniballs or rod ends) are used on both ends of a trailing arm. There are a few ways to counteract this negative trait. One is to use a wobble-stopper uniball at the frame end of the link. The wobble stopper is simply a uniball assembly that features an external twist limiter, usually in the form of a custom-machined spacer made from nylon or Delrin. Blitzkrieg Motorsports and Kartek Off-Road both offer wobble-stopper uniball assemblies as stand-alone builder parts.

15. The S.I. Motorsports trailing arms are things of TIG-welded beauty. One advantage to trailing arms in which the shocks mount above the center line is that the shocks’ rod ends do not have to be the extended-length type. Being able to use conventional shock rod ends makes life a little simpler when it comes to ordering shocks or finding secondhand shocks compatible with these trailing arms.

16. The S.I. trailing arms use a Delrin bushing at the frame end. Delrin is self-lubricating and long lasting. Delrin bushings control trailing arm twist and allow the shocks to mount above centerline. This is a proven system that’s been on the market for well over a decade.

17. Urethane bushings at the frame end are another viable option if your shocks mount above centerline. Urethane is softer than Delrin, and it’s a good choice if your trailing arms flex side-to-side (a common effect when using a wishbone upper link) while they’re cycling up and down. Urethane works best with a regular greasing schedule. .