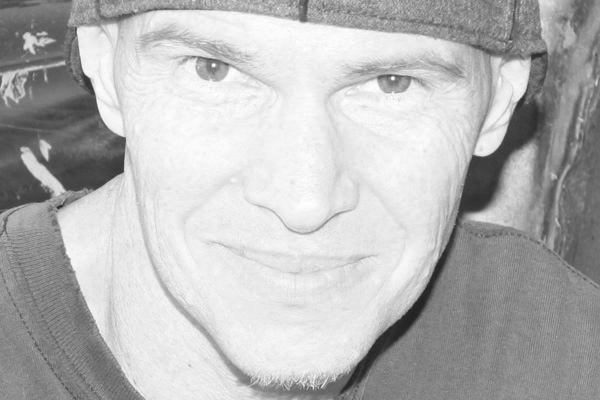
Kevin Blumer
Contributor
Whoever coined the phrase “the devil is in the details” was absolutely right. Once the major parts of a project are in place, it’s easy to sit back and coast for a while. In fact, we recommend taking a breather after each major stage of a project. The trick is to know when to end the breather and get back to the project. Wait too long and the project could be condemned as an eternal almost.
Unfinished projects are a burden. As such, it was time to make a last push and attend to those devilish details.

Even though a bolt-on, ready-made winch bumper would have been easier and quicker, this exercise has provided a chance to hone existing fabrication skills and develop new ones. The modular nature of the complete system means one person can install the whole thing, piece by piece, without an engine hoist or an extra set of hands.
Step By Step

We left off last time in the middle of building a connector strut between the bumper and the A-arm crossmember. The strut will add support to the bumper and will add protection for the radiator and the air-conditioning condenser.

Two-bolt flanges work well for applications like this. The flanges were welded on the front and back sides to eliminate opportunities for water to pool and cause rust.

After we’d welded all the tubing joints, we chose to enclose the strut with plates on the top and bottom. The bending die made a perfect template.

Short pieces of capped tubing were then welded in the open ends of the strut. Now, the strut is completely sealed, and the capped stubs will further strengthen the assembly.

Here are the adjacent parts of the two-bolt flange system. The larger, 1 3/4-inch tubes slip over the 1 1/2-inch tubes and will allow an ideal fit to be created.

The plates were cut out using our Milwaukee/Swag tabletop bandsaw system. Welding the plates on was a tedious, yet straightforward, endeavor.

As seen here, the 1 3/4-inch tubes slid forward until they contacted the main bumper and then multiple tack welds were placed. The bumper and strut were then removed from the 4Runner so final welding could take place on the bench.

Turn-signal brackets were created from three tabs to which a mounting plate will be bolted. An angle finder helped get the tabs to symmetrical angles before being tack welded.

The outer ends of the main tube were cut off at an angle, and an oval cap was welded on. The caps seal the main tube and add a touch of class.

Lateral spacing was kept consistent with a simple jig made from flat bar and angle iron.

This bumper is ready for the distant future, too. These tabs and rod end will allow the top of the bumper to tie into an eventual engine cage through the radiator core support.

The three turn-signal mounting tabs are ready for the turn-signal plates. We’ll create those later on.

The project came to a point where it seemed there’d be no more welding to the main structure. As such, both the bumper and the support strut were treated to a durable, attractive powdercoat finish.

D-ring mounts needed to be created and welded on. There’ll be one on each side of the Warn fairlead.

The revised D-ring brackets were simpler and easier to make. First, a piece of 1-inch, .120-wall seamless tubing was notched for the 1 1/8-inch D-ring tube.

Seamless tubing of 1-1/8-inch, .120-wall dimensions fit perfectly over the 7/8-inch D-ring pin.

The two tubes were secured on the mini welding table and tacked together.

The first plan called for four plates, each with two holes and multiple cuts on the band saw. The result would be nice, but was too labor-intensive even for this project. It’s easier to brainstorm with paper templates than with metal.

The notched tube was then welded to the D-ring tube. After that, the base of the bracket was welded to the winch mount. We had to clean paint off in order to weld the D-ring brackets on. We’ll touch those sections up later rather than stripping and re-painting the whole winch mount.

The two tubes seemed like an adequate bracket, but considering the forces that might be placed on the D-ring mount a little overkill was called for. A piece of 1-inch wide, 1/8-inch flat stock was sliced down the center.

The turn-signal plates were made using 1/8-inch aluminum for the center and steel tabs on each end. There’s one turn signal and one foglight per side.

The newly created strips were fitted and welded around the outside of the D-ring bracket, adding strength without adding bulk or complexity.

Our winch’s solenoid box had to be relocated. A custom-fabricated bracket bolts between the solenoid box and the bumper system’s main crossmember. As it now sits, the solenoid is tucked out of the way, yet is easily accessible when needed.