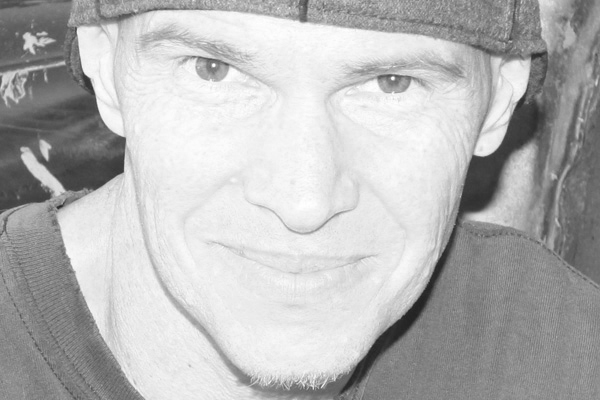
Kevin Blumer
Contributor
Last time (November 2013) we got our 4Runner bumper project well underway, enough so the structure was stitch-welded to a section of heavy-wall box tubing to keep it stable during final welding. The tactic worked. Once all the welds were completed, it was time to add an extension to the lowermost cross tube, and build a removable support strut to tie the bumper into the frame's A-arm crossmember.
This bumper project has proven extensive, but the end is in sight. Once the support strut is finished, the biggest hurdles will have been cleared. Left to go: light-mounting tabs, a bracket for the Warn 9.5 xp-s winch solenoid, caps for the main tube, turn signal tabs, and tie-in brackets for a future roll cage. When the metalwork is complete, this sucker is getting treated to a durable, attractive powder-coat finish.
Step By Step

The lower extension starts with a pair of tabs and a cross tube. The cross tube indexes into the tabs.

A metal table with a straight edge would have been better for mock-up, but this beat-down wooden table had to suffice. Hindsight says I could have made the process a little more accurate by placing some flat metal stock along the edge.

The first order of business was to tack weld a temporary shear plate between the main tubes.

With the shear plate in place, the inner face of the tabs was welded onto the tubes.

The temporary shear plate was removed using a Dremel tool with a small cutoff wheel mounted in the chuck. Filler plates were added between the tubes, and the outside edge of the end tabs was welded onto the upper main tube. The next step is to build the strut that will connect the bumper with the frame’s A-arm crossmember.

The temporary shear plate was removed using a Dremel tool with a small cutoff wheel mounted in the chuck. Filler plates were added between the tubes, and the outside edge of the end tabs was welded onto the upper main tube. The next step is to build the strut that will connect the bumper with the frame’s A-arm crossmember.

The first step was to bend the support strut’s main tube. We’re going for a U-shape, so we need a 180-degree bend. Just like last time, it was helpful to add a label to the bender. The bend will form to the left, and the right-hand section of the tube will stay static. We turned to M-Tech Supply for this bender and the matching dies.

The bend got close to the needed 180 degrees, but we stopped just short because we felt gun-shy about over-bending the tube by mistake. Remember: Tube bending is a skill just like welding. Practice and experience are gained one bend at a time.

There’s a cross tube in the way between the bumper and the A-arm crossmember. As such, the strut needs to bend in order to clear the cross tube. Each side of the U-shape needs an identical bend, so we made sure that the U-shape was square to the bender by checking with a framing square.

You can make repeatable bends if you take notes of the distance between the ram housing and a mark on the bolt head. This is a more accurate method compared to using a degree wheel alone. Our bender is powered by a Swag Offroad bracket kit and a Harbor Freight air/hydraulic ram.

Here’s the first leg bent. Now the other leg needs an identical bend.

Making the second bend was trickier than the first. The second bend needed to be in the same plane and needed to start at the same point. First, the U-shape was squared in the bender by checking again with the framing square.

By writing down the distance between the apex of the U-shape and the edge of the die’s holding strap, we were able to place the second bend in the same location as the first.

By writing down the distance between the apex of the U-shape and the edge of the die’s holding strap, we were able to place the second bend in the same location as the first.

It took three bends, quite a bit of measuring, and an equal amount of head-scratching to produce this “simple” shape.

Extra tubing will strengthen the end of the U. A ratchet strap was able to pull the ends of the tubes together, making up for the final few degrees needed to reach 180.

A mini welding table, multiple clamps, and several machinists’ blocks kept things in place during tack welding.

This bracket bolts to the A-arm crossmember. The apex of the U-shape will be welded to it.

Here’s the support strut mocked into place. The legs of the U-shape will be trimmed to length so they slip directly behind the bumper’s lower extension. You can also see the cross tube below the radiator. It’s what necessitated the additional bends.

Need a project before you build a bumper? Fabricating a welding cart is an excellent way to go. The stainless steel tank for the water-cooled torch (below the welder) was another fabrication project.

We’ve used Swag Offroad’s tabletop bandsaw conversion system in conjunction with a Milwaukee hand-held bandsaw for several years now. It’s getting updated with a new bandsaw mounting plate that places the saw at a more optimal angle. The plate also fits more closely around the blade, so fewer scraps can fall through into the blade’s guide rollers. The Swag/Milwaukee bandsaw system is excellent for cutting out custom brackets.